
BIM Documentation: Understanding need for BIM standards, procedures, and other documents
Do you know the term “Bus Factor”? This concept is more well-known in the IT industry, and I think it will be increasingly used in the construction industry over time (well, we are going to use it to better explain BIM documentation). Why? Because we are increasingly programming and automating projects to make our lives easier.
Bus Factor is a measure of risk resulting from a lack of sharing information and skills among team members. In simplified terms, it is the number of people who would need to be “run over by a bus” in order for the project to become impossible to continue.
Of course, this should not be taken literally, but rather understood that the Bus Factor refers to any random event that could cause a key person in the project to disappear, and as a result, the project would be unable to continue or introducing a new competent person would be very expensive and risky.
Bus factor in BIM
In the IT industry, to prevent such situations, a project is divided into a greater number of tasks with smaller scopes. And more people are involved who try to ensure that others know exactly what each person is doing on the project.
It is also a good practice to use a Guidebook, which is essentially a project guide. You will find good practices used in programs – problem-solving instructions that arise from project to project and are typical for a given industry and project. The Guidebook aims to systematize work and prevent reinventing the wheel.
This article will explain why it is worth creating Standards, Procedures, and Guidebooks in a design office or a construction company and what such a document should contain.
Below are brief descriptions of the differences between each of these documents.
PSPG (Policy, Standards, Procedures, and Guidelines)
Have you ever experienced a situation where during a two-week absence of a colleague, you had to “jump in” on a project to replace another team member and waste a whole week getting familiar with the program and project information?
The typical question in such a case is: “What and where can I find it, and why was it designed this way?” It sounds like a nightmare, doesn’t it? However, for people on the other side who know they will face chaos when they return from their “break,” it is also an uncomfortable situation that causes feelings of guilt, worse recovery, stress, etc.
To avoid employee frustration, save project budgets, and facilitate the onboarding of new or temporary employees on a project, standards, procedures, and guidelines are used. Many of you may have encountered these terms, but we often use them interchangeably or inappropriately.
In short: policy is a unified high-level declaration (given by the CEO and management) throughout the organization. A standard is the lowest level of control that cannot be changed, while a procedure is a sequence of steps. Guidelines are simply a review of how a task can be executed.
Basic assumptions of the PSPG
Policy [Strategy] Document – contains the general idea, and management’s intentions in creating rules to ensure fair treatment, discipline, and compliance, for example, Dress Code Policy, and Internet Policy.
Standard – a set of mandatory rules supporting the policy. It is the level of quality that we want to achieve, for example, the standard of final drawings. Standards have high authority and may include procedures and requirements. A standard is set by the organization, and employees do not have the ability to make changes.
Procedure – a requirement, checklist of items, a series of individual steps that must be followed to achieve the standard. It is created by employees who are experts in a particular field.
Guideline – guidance, advice, and best practices that help achieve a goal, such as showing behavior in a particular situation. They are recommended but not mandatory.
Documentation in the design and construction industry
Each company has its own specifics of project creation: its own styles, tables, and work methodology. Some companies specialize only in one industry and outsource the rest. Some manage the entire project from concept to construction work, so there is not only one solution to how documents such as strategies, standards, procedures, and guidelines should look.
Once we have answered why, what, and how we need to implement in order to streamline the process, it is worth outlining a team of people who will be responsible for this.
- Who is the documentation addressed to?
- Who will be responsible for the creation and updates of the documentation?
The PSPG documentation should contain concise and practical information. The recipients of the documentation are designers and 3D modeling specialists. This applies to both new and existing employees, industry managers who supervise work, and engineers who are responsible for the quality of information contained in the models. These recipients should also actively participate in the process of updating and creating documentation.
Sometimes, some elements of the standard and procedures (e.g., model naming conventions) may be imposed by the client and may then vary depending on the project. However, the process of creation, order, and organization should be set by the design office or construction company.
Practical example – description of creating a wall in 3D program
It is worth noting that 3D programs give us many more possibilities for interpreting the selected path of creating elements than 2D programs. For example, we can create a wall that consists of one part but is divided inside into a plinth, a base, and a cornice, or create three separate walls named plinth, base wall, and cornice.
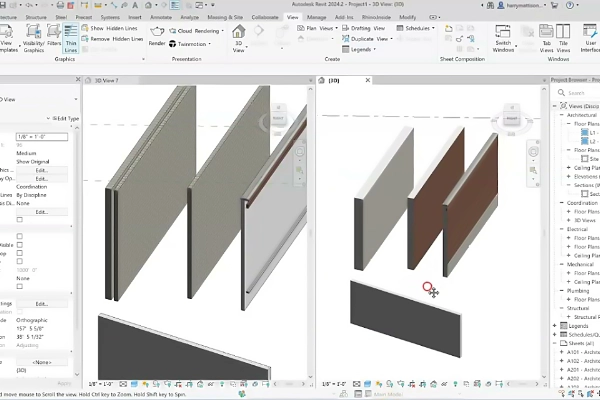
Each method has its pros and cons. Three separate walls can be problematic when we want to move the wall, and we should remember about two other elements that need to be checked if they are moved automatically or need to be adjusted manually.
The program usually helps us with this and informs us about the elements that are “floating”. But as we know, we don’t always have time to check 3D models, for example, if we only provide specific flat 2D drawings for the client. On the other hand, the 3-in-1 wall is for more advanced users and requires more time and analysis in the initial phase, but in the later phase, it facilitates changes.
This is a simple example, but in a large company that works on many projects, details and time matter. It is good to choose one way of creating walls (and other elements such as floors, columns, windows, etc.) and stick to it when modeling.
Such information should be included in the Guideline as advice on how to skillfully model to facilitate editing the model. In the procedure, we would describe the name of the wall, which should be defined as, for example, Wall_Plasterboard_10cm.
Detailed strategies, standards, procedures, and guidelines based on a simple model of a house will be discussed in upcoming articles! We will take a closer look at the benefits of having documentation in the company that reduces the “Bus Factor” risk.
The Importance of Consistency in BIM Standards
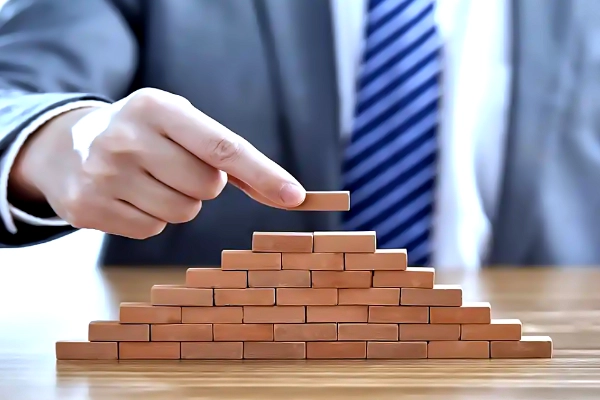
In the fast-paced construction industry, consistency is crucial for maintaining efficiency and quality. By implementing a uniform approach to creating and managing models, teams can minimize errors, miscommunication, and delays. For instance, when working on large-scale projects with multiple disciplines involved, adherence to a set standard ensures that the deliverables from each team align seamlessly.
This consistency simplifies the review process, reduces the time spent on coordination, and ultimately leads to a higher-quality output.
Another vital benefit is the ability to track accountability. When standards and procedures are well-documented, it becomes easier to identify areas where workflows are deviating and implement corrective actions. This traceability is especially beneficial in multidisciplinary projects where the risk of oversight is higher.
Benefits of BIM Documentation
BIM documentation does more than just organize work; it creates a repository of knowledge that empowers teams to work smarter. Here are some of the key benefits:
Enhanced Collaboration
Well-documented standards foster better collaboration among team members. Whether it’s architects, structural engineers, or MEP specialists, a common framework ensures everyone is on the same page, reducing conflicts and improving efficiency.
Onboarding Made Easy
Bringing new hires or temporary employees up to speed is simpler when the company has clear documentation in place. New team members can quickly familiarize themselves with workflows and tools, reducing the learning curve and minimizing disruptions to ongoing projects.
Future-Proofing
A robust PSPG framework helps companies adapt to new technologies and methodologies.
For example, as BIM software evolves, documented procedures and guidelines can be updated to reflect new features or industry standards, ensuring the company remains competitive.
Improved Quality Assurance
Standards and guidelines act as checkpoints for quality assurance. They ensure that models and drawings meet the desired level of accuracy and completeness, reducing the likelihood of costly errors or rework.
Final Thoughts
Developing and maintaining BIM standards, procedures, and guidelines is an investment in the long-term success of your organization.
By reducing the “Bus Factor” risk, improving collaboration, and ensuring consistent quality, BIM documentation helps teams navigate the complexities of modern construction projects. Want to learn more? Book your free consultation today!